Vákuumöntési szolgáltatások
- Azonnali árajánlat áll rendelkezésre
- Tartós alkatrészek gyártásszintű minőséggel
- Alacsony költség és gyors átfutás a kiváló minőségű műanyag alkatrészekhez
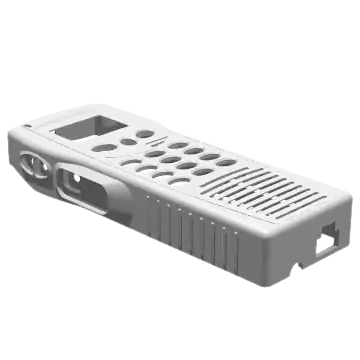
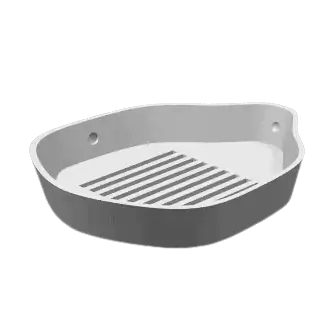
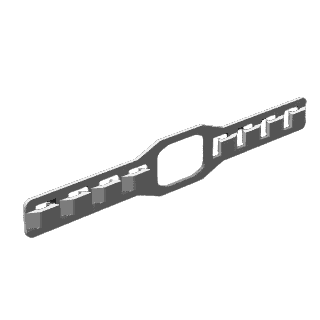
Indítson egy új öntési árajánlatot
STEP | STP | SLDPRT | STL | IPT | 3DXML | CATPART | PTC | PRT | SAT | PDF
Vákuumöntési folyamat és kapacitások
A vákuumöntés a végső felhasználású, rideg, rugalmas és gumi alkatrészek gyártásszintű minőségben történő előállítására szolgáló technika. Ez az eljárás 3D nyomtatású mestermintát és szilikon öntőformákat alkalmaz, hogy kiváló minőségű, kis sorozatú, akár 2000 mm hosszúságú alkatrészeket állítson elő. A vákuumöntésű alkatrészek kész méretei a mestermodell pontosságától, az alkatrész geometriájától és az öntési anyagtól függenek.
Gyakran használnak vákuumöntésű alkatrészeket, ha színre, felületminőségre és szívósságra van szükség. A vákuumöntés tökéletes alternatíva a betétes fröccsöntéshez kis volumenben, és sokféle anyaggal kompatibilis. A poliuretán öntvény a 3D nyomtatású gyors prototípus-készítés és a fröccsöntés közötti áthidaló szerszámok kialakításához is használható a minőség, a költségek és az idő hatékony kiegyensúlyozása érdekében. A vákuumöntésű alkatrészek lehetnek átlátszóak, színillesztettek, festettek is, beépített betétekkel is rendelkezhetnek és akár egyedi kidolgozásúak is lehetnek.
A vákuumöntés alkalmazásai
Kis volumenű gyártás
A vákuumöntésű alkatrészek tökéletesek a kis mennyiségű gyártáshoz—ha a volumenek nem indokolják a fröccsöntő szerszámokba történő befektetést—és az első gyártású alkatrészekhez, amelyek hetekkel azelőtt elkészülhetnek, mielőtt a gyártási szerszámozás készen lenne.
Fejlett prototípus-készítés
A vákuumöntési folyamat és a hozzá tartozó viszonylag olcsó szerszámozás egyszerűvé és gazdaságossá teszi az esetlegesen szükséges tervezési módosításokat. Ráadásul különböző anyagok használhatók ugyanazzal az öntőformával, ami lehetővé teszi, a tervek különféle anyagokkal történő tesztelését.
Piaci tesztelés
A végfelhasználói funkcionalitás és a kiváló minőségű kidolgozások ideálissá teszik a vákuumöntésű alkatrészeket a fogyasztói teszteléshez, a felhasználói értékeléshez és a koncepciómodellekhez. Az uretán öntési eljárás használata azt jelenti, hogy a módosítások gyorsan beépíthetők további tesztelés vagy piaci bevezetés céljából.
Miért a Xometry a megfelelő partner a vákuumöntési projektjeihez
Átfutási idők
Az alkatrész tervezésének összetettségétől és a prototípus kívánt felületi minőségétől függően a vákuumöntés 15-25 napot vehet igénybe.
Gyártási volumen
A vákuumöntés a legalkalmasabb a kis volumenű, akár 20 egységből álló, egyetlen öntőformából készült prototípus elkészítéséhez. Több egységek esetén további öntőformákra lesz szükség, és a projekt költségei megemelkednek.
Anyagválasztás
Válasszon több mint 15 műanyag közül az öntési projektjeihez, és kérjen azonnali árajánlatot.
Szakképzett mérnöki csapat
Tapasztalt öntőmérnöki csapatunk végigvezeti Önt a folyamat minden lépésén.
Kérjen árajánlatot alkatrészeihez most
CAD-terv feltöltéseMinden feltöltés biztonságos és bizalmas.
Vákuumöntési anyagok kiválasztása
- PU8150, ABS-szerű
- PU8263, ABS-szerű UL94-V0
- PX223HT, ABS-szerű magas hőmérsékletnek ellenálló 120
- UP6160, ABS-like magas hőmérsékletnek ellenálló 200
- UP4280, ABS-szerű
- PX5210HT, PMMA / Akril-szerű áttetsző
- PX522HT, PMMA / Akril-szerű
- 8550, PP-szerű
- UP5690, PP-szerű
- PX527, PC-szerű
- PA 6 (DPI 2180)
- PU84000, Gumiszerű
Vákuumöntési tűrések
A vákuumöntési tűrések a rész méreteitől és a tervezési összetettségtől függnek. Az alábbi táblázat példákat tartalmaz különböző mérettartományok alapján*:
Méretek (mm) | 0 — 25 | 25 — 50 | 50 — 75 | 75 — 100 | 100 — 125 | 125 — 150 |
Tűrés (mm) | ±0,3 | ±0,35 | ±0,4 | ±0,45 | ±0,5 | ±0,55 |
*A megadott értékek tájékoztató jellegűek. A tűréseket egyedileg kell meghatározni minden vákuumöntési projekt esetében, a konkrét alkatrész 2D rajzai és CAD modelljei alapján. A 150 mm-nél nagyobb részekhez kérjük, mellékeljen 2D rajzot, és beszélje meg a tűrési követelményeket az ügyfélszolgálati menedzserével.
Leírás | Tűrési megjegyzések |
Távolságméretek | A szabálytalan vagy túlzottan vastag geometriák eltéréseket vagy elhajlást okozhatnak a zsugorodás következtében |
Felületi minőség | A felület kidolgozását kívülről szatén vagy matt felületre simítják. Növekedési vonalak lehetnek a belső vagy a nehezen hozzáférhető elemeken. A polírozást vagy az egyedi kidolgozást egyértelműen kell meghatározni, és meg kell állapodni benne a megrendeléskor |
Tulajdonság meghatározása | Az éles sarkok és a szöveg kissé lekerekítettnek tűnhetnek |
Méretajánlás | Akár 2000 mm hosszú vákuumöntésű alkatrészeket is tudunk kínálni |
A vákuumöntés alapjai
A vákuumöntés olyan gyártási folyamat, amely végső felhasználású, rideg, rugalmas és gumi alkatrészeket biztosít gyártásszintű minőségben. A vákuumöntési folyamat Polyjet vagy SLA 3D nyomtatású mestermintát alkalmaz, hogy olyan szilikon öntőformát hozzon létre, amely kiváló minőségű, kis sorozatú alkatrészeket állít elő a kis volumenű fröccsöntés költséghatékony alternatívájaként.
A vákuumöntés abban hasonló a fröccsöntéshez, hogy üreges szerszámra van szükség a végső alkatrészrész formájában. A fő különbség az, hogy a vákuumöntésnél szilikonból készült „puha” öntőformát használnak, míg a fröccsöntésnél „kemény” fém öntőformát használnak, amelyet CNC-vel munkáltak meg.
Ez a puha öntőforma gyorsabban elhasználódik, ami a vákuumöntés fő hátránya. Az eljárás azonban jelentősen olcsóbb kis volumenű és prototípusos műanyag alkatrészek esetén, amelyek gyártásszintű minőséget és felületi kidolgozást igényelnek.
A vákuumöntés folyamata 3 fő lépésből áll:
- A mesterminta: Az első lépés magában foglalja a végső alkatrész mestermintájának létrehozását additív gyártási folyamat segítségével. A leggyakrabban alkalmazott nyomtatási eljárások a Polyjet 3D vagy a sztereolitográfia (SLA) 3D, mivel képesek nagy felbontású és természetesen sima kidolgozású alkatrészek előállítására. A mestermintát jellemzően kézi kidolgozású, hogy optimális felületi részletet érjenek el az öntőforma-szerszám létrehozása előtt.
- Formázás: A második lépésben a 3D nyomtatású mestermintát folyékony szilikonba burkolják, amely megkeményedik a minta körül, és a szilikon magába zárja a nyomtatott alkatrészek összes elemét. Amikor a forma megkeményedik, két különálló félbe vágják, és eltávolítják a mestermintát vagy a 3D nyomtatású alkatrészt. Ez egy pontosan olyan alakú belső üreget hagy maga után, mint az alkatrész.
- Öntés: A vákuumöntési folyamat utolsó lépésében szilikont öntenek a szilikon öntőformába, majd az öntőformát egy kamrába helyezik, hogy segítsen eltávolítani a légbuborékokat a folyékony anyagból. Az átlátszatlan alkatrészek esetén a kamra jellemzően nyomás alatt van. Átlátszó alkatrészek esetén a kamra jellemzően vákuumot húz, hogy csökkentse a buborékokat és növelje az átlátszóságot. A megkeményedést követően a két szilikon felet szétválasztják, és az újonnan kialakított alkatrészt eltávolítják. Ezt a folyamatot a kívánt mennyiség eléréséig ismétlik meg.
Az egyik legfontosabb különbség a vákuumöntés és a 3D nyomtatás között az anyagteljesítmény és a minőség. A vákuumöntés nagyobb teljesítményű anyagokat kínál, amelyek jobban utánozzák a kereskedelmi termékekben alkalmazott anyagokat. Ráadásul az illeszkedés és a kidolgozás gyakran jobb a vákuumöntésű alkatrészekkel. Ha az anyag teljesítménye és megjelenése fontos Önnek, akkor komolyan meg kell fontolnia a vákuumöntést.
A döntő tényező a vákuumöntés és a fröccsöntés között az a mennyiség. A vákuumöntés kiváló lehetőség nagyon kis mennyiségű (pl. 50 darab) gyártásminőségű alkatrészek esetén. A vákuumöntéssel összehasonlítva a fröccsöntésnek magasabbak az előzetes szerszámozási költségei, amelyet talán nem indokolhat a kis mennyiségű üzem. Ügyfeleink a vákuumöntést gyakran lépcsőfok gyanánt használják, hogy teszteljék és finomítsák a tervezést, mielőtt fröccsöntő szerszámba ruháznának be.