Before one venture into the manufacturing business, it is paramount to select the best machine. One can start his own business with one’s CNC machine or partner up with manufacturing companies like Xometry Europe. This article aims at providing an overview on how to choose a CNC machine for business.
Types of CNC machines
There are mainly five types of CNC machines. They vary in the method of operation.
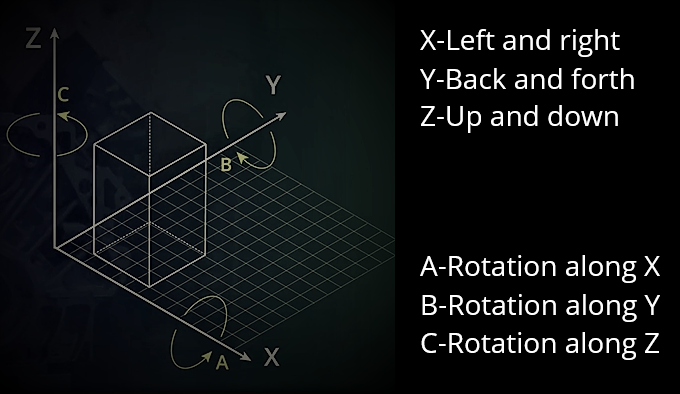
CNC Lathe Machine
The Lathe CNC machine consists of a lathe that adjusts and moves the material into the required position as programmed on the computer. The machines rotate materials against the tool while in operation and thus subtractively manufacture the required part. Usually, they have a lesser number of axes than milling CNC machines, thus making them smaller and more compact.
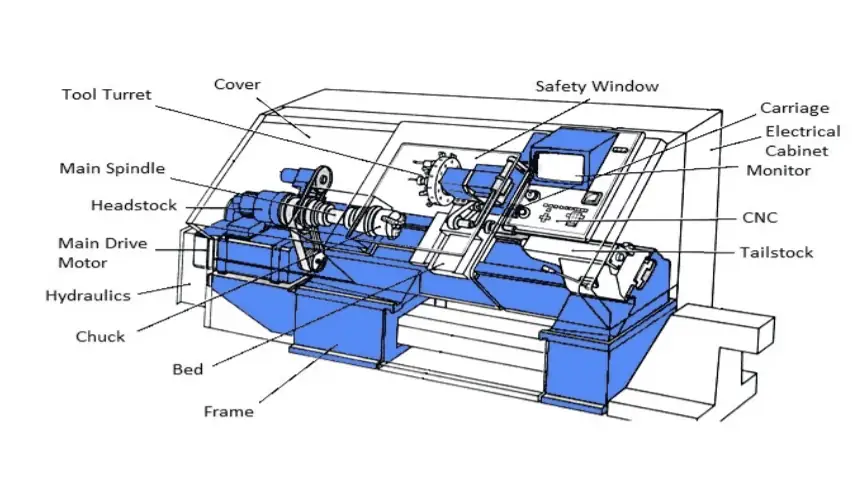
There are two main types of CNC lathes:
Fixed head CNC lathe (Conventional type)
In a conventional fixed head lathe, there is a fixed headstock. The workpiece is held in the chuck and extends into the machine enclosure as a cantilever or can be supported on the end for the tailstock. The tool moves towards it, performing operations like facing, threading etc. The only difference is, this machine is CNC controlled. A fixed head lathe machines bigger and harder items size above 20mm and are generally suitable for fat and short items.
Sliding head CNC lathe (Swiss type)
Sliding head lathes allow the workpiece to move in the Z-axis while the tool remains stationary. This is unlike traditional lathes where the workpiece remains in position while the tools move around it. The benefit of this is increased precision and reduced process time. Workpieces smaller than 33mm are naturally ideal. It is suitable for long, thin and delicate parts. This lathe acquires more precision and intricate details compared to the conventional machine.
CNC Milling Machine
CNC milling machines are one of the most common and widely used machines. They feature built-in tools for cutting and drilling. Materials to be machined are placed inside the CNC milling machine, followed by the computer guiding the tools to cut or drill it. These multi-operational machines are available from 3 to 6-axes.
There are two common types of CNC milling machines based on the alignment of the spindle axis, i.e, Vertical milling and horizontal milling machines.
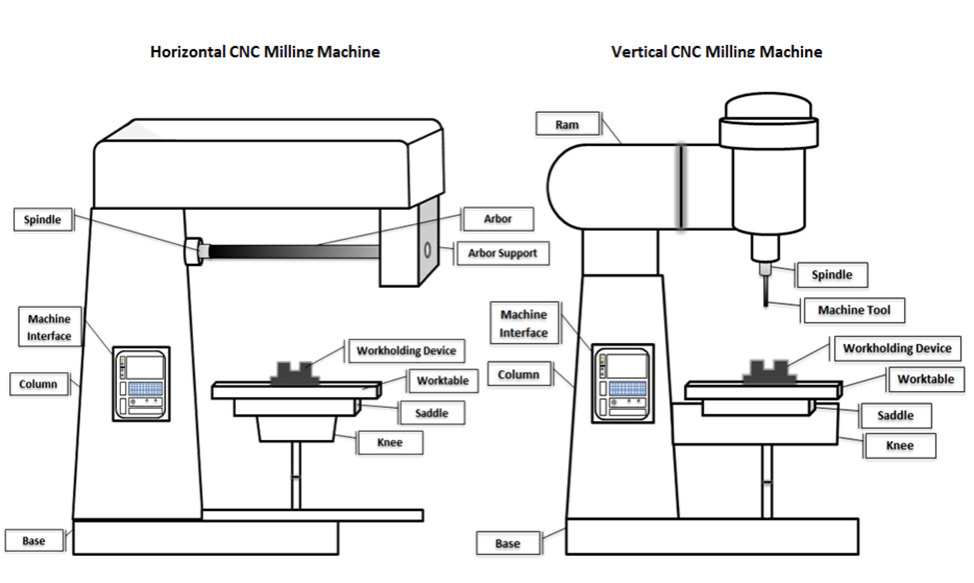
Comparison between the two milling machines:
Vertical milling machine | Horizontal milling machine |
The spindle axis is aligned vertically | The spindle axis is aligned horizontally |
Usually have long and thin cutting tools | Usually have short and thick cutting tools |
Ideal for detailing, accuracy and precision. Best for single plane operations | Ideal to cut bigger, heavier and deeper cuts and grooves. Works on multiple planes at the same time |
Slower in operation comparatively | Faster than vertical as it can reach three faces in one cycle |
Reduces tool life | Increases tool life |
Poorer surface quality | Excellent surface quality |
Improper chip removal | Best in class chip removal and separation from the work area |
Cheaper, lighter and also occupies less space | Costly, sturdy, heavy and occupies more space |
Best for small businesses which focus on milling intricate detailing and minute operations | Best for businesses that focus on big and heavy materials and batch production due to its speed |
CNC Plasma-Cutting Machine
Plasma- Cutting CNC machines feature a high-powered plasma torch that achieves about 28,000 degrees Celsius which is about five times the temperature achieved by electric welding machines. This temperature helps the plasma torch penetrate through hard metals. The plasma torch is controlled by the computer programme.
CNC Laser-Cutting Machine
Laser CNC cutting machines are almost similar to plasma cutting machines but the former utilises a laser instead of a plasma torch to cut the materials. Lasers usually offer higher cutting accuracy but are not as strong as plasma cutting machines. The typically used lasers are Co2, Neodymium(Nd) or Yttrium-Aluminium-Garnet(Nd-YAG).
CNC Electric Discharge Machine
Electric discharge can deform a material on exposure and erode it. CNC Electric discharge machine produces controlled electric discharge sparks to reshape materials. Hence it is also called a spark CNC machine. The machine has an anode and a cathode. The material is placed between the electrodes and the amount of discharge is controlled by the computer.
Considerations on buying a CNC machine
Purchasing a CNC machine has to be done carefully as it costs a lot. From initial purchase costs to programming to labour costs to maintenance costs, there is a lot to take into account. Apart from the costs, there are a lot of factors to take into account
The goal of the machine
One must carefully think about what services one wishes to provide. A lathe is ideal for facing, turning, chamfering, threading, knurling and boring. A milling machine can also perform its operations along with fillet making, slot cutting, drilling efficiently. The latter is almost twice the price of the former. It up to the buyer’s discretion on what he wants to buy and cater to the customers.
Cost incurred
Prices vary depending on the type, specification and condition of the machine. A good CNC machine from a quality brand usually has a good life span. They even offer lifetime warranty and other customer-oriented services without breaking the bank. It is advised to do thorough research before picking one. It is also advised to buy a machine which has good availability of spare parts and is easily repaired by the technician. Cost doesn’t only mean the machine cost but also the labour, maintenance etc.
Machine weight
The common materials utilised in CNC machine build are aluminium, composite polymer, and cast iron. If you consider a durable and sturdy machine for tough and heavy tasks, cast iron built is the best. Lighter and small operations can be done on the other lighter machines.
Right CNC system selection
A CNC machine can be installed and equipped with a variety of CNC software and systems. A particular system improves the performance and quality but also increases the pricing. Different companies have different systems with varying specifications. It should be selected based on the machines’ main performance. Once the requirements of the buyer are met, check for pricing. It is always better to consult an experienced manufacturer in the selection of the CNC system.
Main specification selection of a CNC machine
The stroke range or length of multiple CNC axes and the spindle motor power are considered the main specifications of a CNC machine. A similar machine can have different configurations in terms of main motor power. Main motor power is directly proportional to the cutting rigidity and spindle high-speed performance of the machine tools. Lighter machines have lesser power compared to the standard ones
Power consumption
Always check the power requirements of the machine. In case the machine needs more, one may need to increase the available power at the workshop which incurs costs.
Conclusion
Buying a CNC is expensive. It is paramount to research before buying one. Sometimes, a used machine might serve the purpose and can be cheap and equally efficient. Which CNC machine to consider and what service does one want to offer is completely up to one’s discretion. With a network of more than 2,000 partners all over Europe, Xometry takes much pride and happiness in welcoming more partners.