Termoformowanie, proces produkcji tworzyw sztucznych, polega na formowaniu arkuszy termoplastycznych w pożądane kształty za pomocą ciepła. Historycznie rzecz biorąc, jego początki sięgają starożytnych praktyk podgrzewania materiałów w celu ich kształtowania, ale współczesne innowacje udoskonaliły jego zastosowanie i poszerzyły jego użyteczność. Obecnie termoformowanie jest niezbędne we współczesnej produkcji ze względu na jego elastyczność, wydajność i opłacalność.
Czym jest termoformowanie?
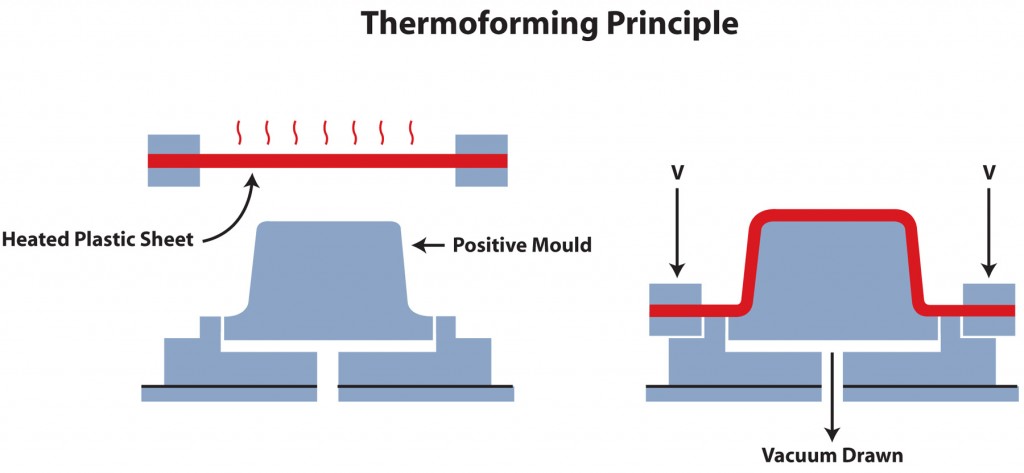
Termoformowanie to wyrafinowana technika produkcyjna polegająca na formowaniu materiałów termoplastycznych w różne trójwymiarowe kształty. Technika ta opiera się na manipulowaniu wrażliwymi na ciepło tworzywami sztucznymi, nadając im pożądany kształt. Materiały termoplastyczne są najpierw poddawane działaniu kontrolowanego źródła ciepła, dzięki czemu stają się giętkie. Po wystarczającym podgrzaniu materiały te są rozciągane na skrupulatnie zaprojektowanej formie.
Aby zapewnić płynne dopasowanie tworzywa sztucznego do formy, przykładana jest siła zewnętrzna, podciśnienie lub ciśnienie. Siła ta gwarantuje precyzję, gwarantując ścisłe przyleganie arkusza tworzywa do każdego konturu i szczegółu formy.
Wszechstronność tej metody jest naprawdę godna pochwały. Nie tylko obsługuje szeroką gamę materiałów termoplastycznych, ale jej zastosowania obejmują różne sektory. Gdy materiał termoplastyczny osiągnie swój ostateczny kształt, kolejne etapy obejmują precyzyjne przycinanie i wykańczanie. Te procedury są dostosowane do specyficznych potrzeb użytkownika końcowego, jeszcze bardziej podkreślając niestandardowe możliwości termoformowania.
Jak działa termoformowanie?
Krok 1 – Wybór materiału
Kluczowy jest wybór odpowiedniego rodzaju tworzywa sztucznego, spełniającego specyficzne wymagania produktu końcowego. O wyborze decydują różne czynniki, w tym trwałość, elastyczność i przeznaczenie produktu. Niezależnie od tego, czy chodzi o termoformowanie cienkościenne, zwykle stosowane w opakowaniach, czy grubościenne w przypadku większych komponentów, wybór materiału ma ogromne znaczenie.
Krok 2 – Ogrzewanie i równomierny rozkład temperatury
Po wybraniu materiału arkusz z tworzywa sztucznego poddawany jest procesowi ogrzewania. Istotne jest osiągnięcie równomiernego rozkładu temperatury na całej powierzchni arkusza. Wszelkie niespójności mogą prowadzić do wad lub słabości produktu końcowego. Istota termoformowania polega na plastyczności tworzyw sztucznych po podgrzaniu. Dlatego też utrzymanie stałej temperatury gwarantuje, że tworzywo sztuczne pozostanie giętkie, co ułatwi bezproblemowe formowanie.
Istnieją różne metody ogrzewania, ale wszystkie mają na celu zapewnienie równomiernej temperatury. Ogrzewanie konwekcyjne, promiennikowe i kontaktowe to standardowe praktyki, a każda z nich ma specyficzne zalety. Wybrana technika często zależy od rodzaju tworzywa sztucznego i zastosowanego termoformowania o określonej grubości.
Równomierne ogrzewanie nie polega tylko na osiągnięciu pożądanej temperatury, ale także na zapewnieniu równomiernego rozprowadzenia tego ciepła, zapobiegając powstawaniu gorących punktów i w konsekwencji wad.
Krok 4 – Chłodzenie i przycinanie
Mając w dłoni równomiernie nagrzany arkusz tworzywa sztucznego, następną fazą jest formowanie. Formy do termoformowania odgrywają kluczową rolę w kształtowaniu tworzywa sztucznego w pożądaną trójwymiarową strukturę. Biorąc pod uwagę różnorodność produktów powstałych przy użyciu termoformowania, istnieje wiele rodzajów form i procesów. Formy są zwykle wykonane z aluminium.
W procesie formowania dominują dwie podstawowe metody: formowanie próżniowe i ciśnieniowe. Podczas formowania próżniowego, po umieszczeniu tworzywa sztucznego na formie, podciśnienie wyciąga powietrze, zmuszając tworzywo sztuczne do dopasowania się do konturów formy. I odwrotnie, formowanie ciśnieniowe wykorzystuje sprężone powietrze do dociskania tworzywa sztucznego do formy, zapewniając bardziej szczegółowe i teksturowane wykończenia.
Krok 4 – Chłodzenie i przycinanie
Po tym procesie formowania produkt termoformowany nie jest jeszcze gotowy. Chłodzenie jest niezbędne, aby tworzywo sztuczne zachowało swój nowo nabyty kształt. Plastik musi ostygnąć równomiernie, aby uniknąć deformacji. W zależności od wielkości produktu i rodzaju plastiku, proces chłodzenia może zostać przyspieszony przez powietrze lub wodę.
Po schłodzeniu produkt poddawany jest operacji przycinania. Nadmiar materiału, który nie wchodzi w skład produktu końcowego, jest usuwany. Aby zagwarantować precyzję, stosuje się zaawansowane techniki przycinania, często zautomatyzowane. Ze względu na złożoność produktu i wielkość produkcji powszechnie stosuje się między innymi cięcie laserowe lub sztancowanie.
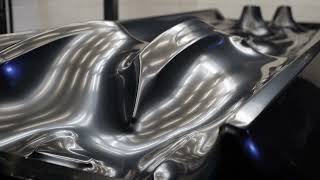
Materiały do termoformowania
Zrozumienie różnorodności materiałów stosowanych w termoformowaniu ma kluczowe znaczenie, ponieważ każdy z nich oferuje unikalne właściwości odpowiednie do różnych zastosowań. Wybór materiału często zależy od pożądanych właściwości i funkcjonalności produktu końcowego.
Najczęściej stosowane materiały w przypadku termoformowania
- PVC/akryl: Materiał ten znajduje szerokie zastosowanie, szczególnie w obudowach urządzeń opartych na mikroprocesorach. Wrodzona wytrzymałość PVC/akrylu i jego zdolność do spełnienia rygorystycznych norm palności UL zwiększają jego atrakcyjność. Co więcej, jego zdolność adaptacji rozciąga się również na estetykę; można go wyprodukować w wielu kolorach i fakturach, aby spełnić określone wymagania projektowe.
- PS (polistyren): Polistyren, czyli polifenyloeten, to polimer termoplastyczny znany ze swoich właściwości elektroizolacyjnych. Jako tworzywo termoplastyczne materiał ten mięknie pod wpływem ogrzewania i można go przekształcać, dzięki czemu nadaje się do ponownego użycia. Jego odporność chemiczna na kwasy i zasady sprawia, że jest to uniwersalny materiał do różnych zastosowań, w tym opakowań ochronnych i izolacji.
- PET (politereftalan etylenu): PET jest podstawą opakowań termoformowanych, włókien syntetycznych i produkcji butelek. Znany ze swojej wytrzymałości i trwałości, PET wymaga suszenia po formowaniu, co jest kluczowym krokiem w celu zapewnienia stabilności i utrzymania kształtu. Powszechne zastosowanie w pojemnikach na żywność i napoje podkreśla bezpieczeństwo i niezawodność tego materiału.
- PP (polipropylen): Polipropylen (PP) jest znany ze swojej odporności na zużycie i stabilności termicznej, co czyni go niezbędnym materiałem w częściach samochodowych, towarach konsumpcyjnych i zawiasach do użytku codziennego. Kluczową właściwością jest jego wyjątkowa zdolność do wytrzymywania ciągłego zginania bez pękania. Dodatkowo odporność na wilgoć, kwasy i rozpuszczalniki sprawia, że PP idealnie nadaje się do produkcji pojemników i rurociągów, a także sprzętu medycznego i laboratoryjnego.
- LDPE (polietylen o małej gęstości): LDPE, charakteryzujący się elastycznością i sprężystością, jest kamieniem węgielnym w tworzeniu produktów wymagających równowagi między elastycznością i wytrzymałością. Odporność na wilgoć i chemikalia sprawia, że idealnie nadaje się do pakowania żywności i pojemników laboratoryjnych. Dodatkowo jego odporność na niskie temperatury gwarantuje niezawodne działanie w różnych zastosowaniach, od pakowania mrożonek po elastyczne rurki i folie rolnicze.
- HDPE (polietylen o wysokiej gęstości): HDPE, znany ze swojej wytrzymałości, jest niezbędny do produkcji dóbr trwałego użytku, takich jak kaski i rury odporne na korozję. Jego odporność na środowisko w połączeniu z wysokim stosunkiem wytrzymałości do gęstości sprawia, że idealnie nadaje się do zastosowań o wysokich wymaganiach, gwarantując trwałość i niezawodność produktów, od mebli ogrodowych po pojemniki do przechowywania.
- PC (poliwęglan): Poliwęglan (PC) wyróżnia się odpornością na uderzenia i przejrzystością optyczną, co czyni go najlepszym wyborem do wyposażenia związanego z bezpieczeństwem, takiego jak szkło kuloodporne, oraz do części samochodowych. Jego wszechstronność rozciąga się na nośniki elektroniczne, takie jak dyski DVD i Blu-ray, demonstrując zdolność do zachowania przejrzystości i trwałości pod wpływem obciążenia.
- PMMA (polimetakrylan metylu): PMMA, słynący ze swojej przezroczystości przypominającej szkło i odporności na promieniowanie UV, jest szeroko stosowany w soczewkach optycznych, akwariach i elementach architektonicznych. Doskonała przepuszczalność światła i odporność na warunki atmosferyczne sprawiają, że jest to preferowany wybór do zastosowań zewnętrznych, wykazując zdolność do zachowania przejrzystości i wytrzymałości w różnorodnych środowiskach.
- ABS (akrylonitryl-butadien-styren): ABS obejmuje szerokie spektrum żywic, dzięki czemu jest wszechstronny w wielu zastosowaniach. Jest solidny i trwały. Może także być dostosowany do norm palności UL. Ta zdolność adaptacji sprawia, że ABS jest często wybieranym materiałem w różnych gałęziach przemysłu.
Tabela porównawcza materiałów do termoformowania
Nazwa materiału | Stabilność cieplna | Odporność chemiczna | Odporność na promieniowanie UV | Sztywność | Koszt |
PVC | Słaba | Słaba | W porządku | Różna | Średnia |
PS | W porządku | Słaba | Słaba | Wysoka | Niska |
PET | W porządku | Dobra | Słaba | Różna | Wysoka |
PP | Słaba | Doskonała | Słaba | Różna | Niska |
LDPE | Słaba | Słaba | Słaba | Niska | Niska |
HDPE | W porządku | Dobra | W porządku | Wysoka | Niska |
PC | Wysoka | Dobra | W porządku | Niska | Wysoka |
PMMA | Słaba | Dobra | W porządku | Wysoka | Niska |
ABS | W porządku | Słaba | Słaba | Wysoka | Średnia |
Dziedzina materiałów termoformowalnych jest szeroka i różnorodna. Dopasowując właściwości materiału do wymagań projektu, można w pełni wykorzystać potencjał termoformowania, gwarantując najwyższą jakość produktu końcowego.
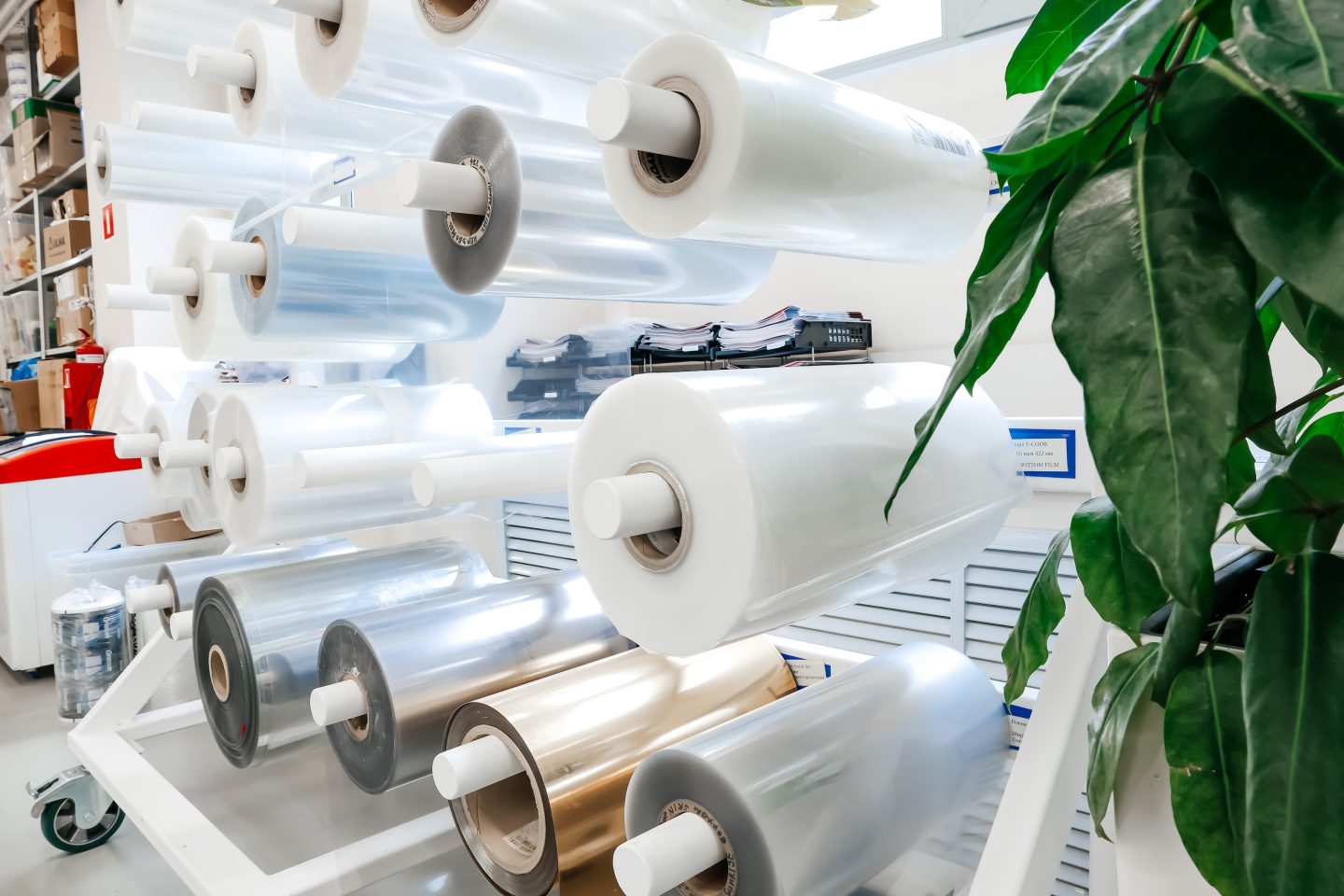
Rodzaje termoformowania
Zrozumienie procesów termoformowania jest kluczowe przy wyborze właściwej metody dla danego zastosowania. Dominują dwie podstawowe techniki: termoformowanie próżniowe i termoformowanie ciśnieniowe. Każda ma swoje zalety, dostosowane do konkretnych wymagań i produktów.
Termoformowanie próżniowe
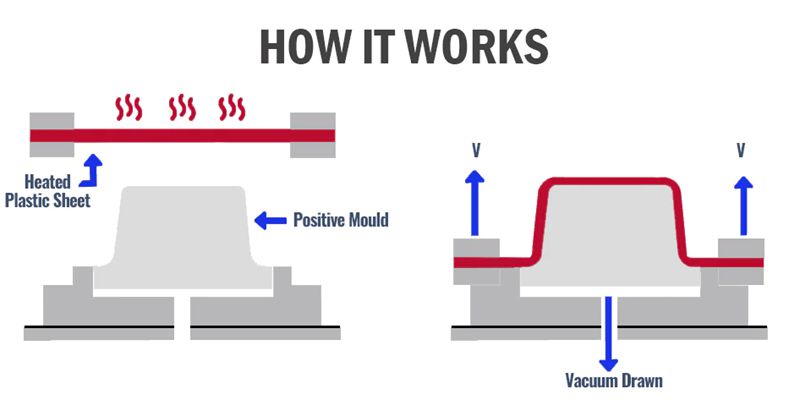
Proces formowania próżniowego, poprzedzający wiele nowoczesnych metod obróbki plastycznej, wyróżnia się jako podstawowa i powszechnie stosowana metoda. Jej wpływ na produkty codziennego użytku jest ogromny i pozostaje integralną częścią kształtowania plastiku w trwałe i sztywne przedmioty.
Jak działa termoformowanie próżniowe:
- Arkusz z tworzywa sztucznego jest początkowo zmiękczany poprzez kontrolowane ogrzewanie
- Ten giętki, podgrzewany arkusz następnie układa się na określonej formie
- Wykorzystując podciśnienie, arkusz jest ciasno dociskany do formy, co daje precyzyjną zgodność kształtu
- Arkusz o obecnym kształcie odłącza się od formy po schłodzeniu, zachowując swoją nową formę
Wraz z postępem technologicznym współczesne formowanie próżniowe obejmuje obecnie skomplikowane sterowniki pneumatyczne, hydrauliczne i termiczne. To wyrafinowanie przyspiesza produkcję i poprawia dokładność produktów końcowych.
Termoformowanie ciśnieniowe
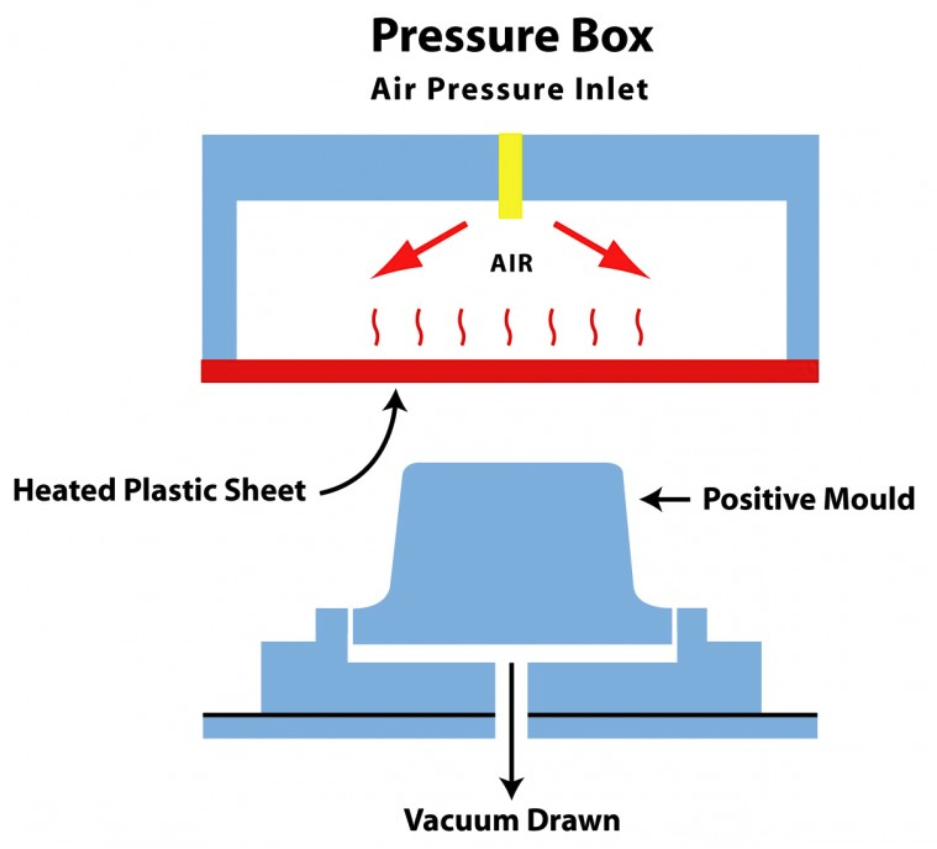
Bardziej współczesna innowacja, formowanie ciśnieniowe, to wyrafinowane podejście do kształtowania tworzyw sztucznych. Proces ten różni się od formowania próżniowego nie produktem końcowym, ale techniką zastosowaną w celu jego uzyskania.
Jak działa termoformowanie ciśnieniowe:
- Jednocześnie stosowane jest podciśnienie i ciśnienie powietrza, wtłaczając arkusz tworzywa sztucznego do formy
- Arkusz z tworzywa sztucznego jest podgrzewany aż do osiągnięcia optymalnego stanu giętkości
- W przeciwieństwie do formowania próżniowego, które wyciąga powietrze, formowanie ciśnieniowe wywiera ciśnienie powietrza. Dzięki temu działaniu tworzywo sztuczne zostaje mocno dociśnięte do szczegółowych konturów formy
- Precyzyjny mechanizm stabilizujący tworzywo gwarantuje optymalną temperaturę, umożliwiając elastyczne, a zarazem precyzyjne tworzenie form
Urok termoformowania ciśnieniowego polega na jego zdolności do wytwarzania komponentów o ulepszonych szczegółach, ostrzejszych krawędziach i doskonałym ogólnym wykończeniu. Kiedy projekt wymaga złożoności i precyzji, najlepszą metodą jest termoformowanie ciśnieniowe.
Chociaż oba procesy termoformowania mają kluczowe znaczenie w branży, ich zastosowanie zależy od specyficznych wymagań produktu. Techniki te, począwszy od artykułów gospodarstwa domowego po komponenty przemysłowe, odgrywają zasadniczą rolę w dostarczaniu wysokiej jakości produktów z tworzyw sztucznych.
Zalety termoformowania
Termoformowanie, kluczowy proces w dziedzinie produkcji tworzyw sztucznych, ma kilka zalet. Te zalety sprawiają, że jest to preferowany wybór w przypadku producentów dążących do wydajnej, opłacalnej i elastycznej produkcji. Oto wgląd w wyraźne korzyści, jakie oferuje ten proces:
- Opłacalność przy średnich seriach produkcyjnych: Termoformowanie wyróżnia się, jeśli chodzi o produkcję dużych ilości. Jego prostota i opływowy charakter oznaczają mniej ruchomych części, co zmniejsza koszty konserwacji. Ponadto stosowane formy są stosunkowo tańsze niż te stosowane w innych procesach, co czyni je bardziej ekonomicznym wyborem w przypadku produkcji na małą i średnią skalę.
- Szybkość produkcji: Nieodłączna prostota procesu gwarantuje szybkie cykle produkcyjne. W porównaniu z metodami alternatywnymi, szczególnie tymi, które wymagają skomplikowanych form lub wydłużonego czasu utwardzania, termoformowanie często okazuje się szybszą opcją.
- Elastyczność projektowania i szybkie prototypowanie: Jedną z cech charakterystycznych termoformowania jest jego wszechstronność w projektowaniu. Producenci nie są zamknięci w sztywnych strukturach projektowych. Zamiast tego mogą szybko dostosowywać i modyfikować projekty zgodnie z wymaganiami. Elastyczność ta rozciąga się również na prototypowanie.
- Efektywność w zakresie odpadów i zużycia energii: Termoformowanie jest szczególnie wydajne zarówno pod względem odpadów materiałowych, jak i wykorzystania energii. Nadmiar materiału z procesu formowania można często zawrócić bezpośrednio do cyklu produkcyjnego, co zmniejsza ilość odpadów. Co więcej, energia wymagana do podgrzania arkuszy tworzyw sztucznych podczas termoformowania jest zazwyczaj niższa niż w przypadku wielu alternatywnych metod, co przyczynia się do zmniejszenia śladu węglowego i niższych kosztów operacyjnych.
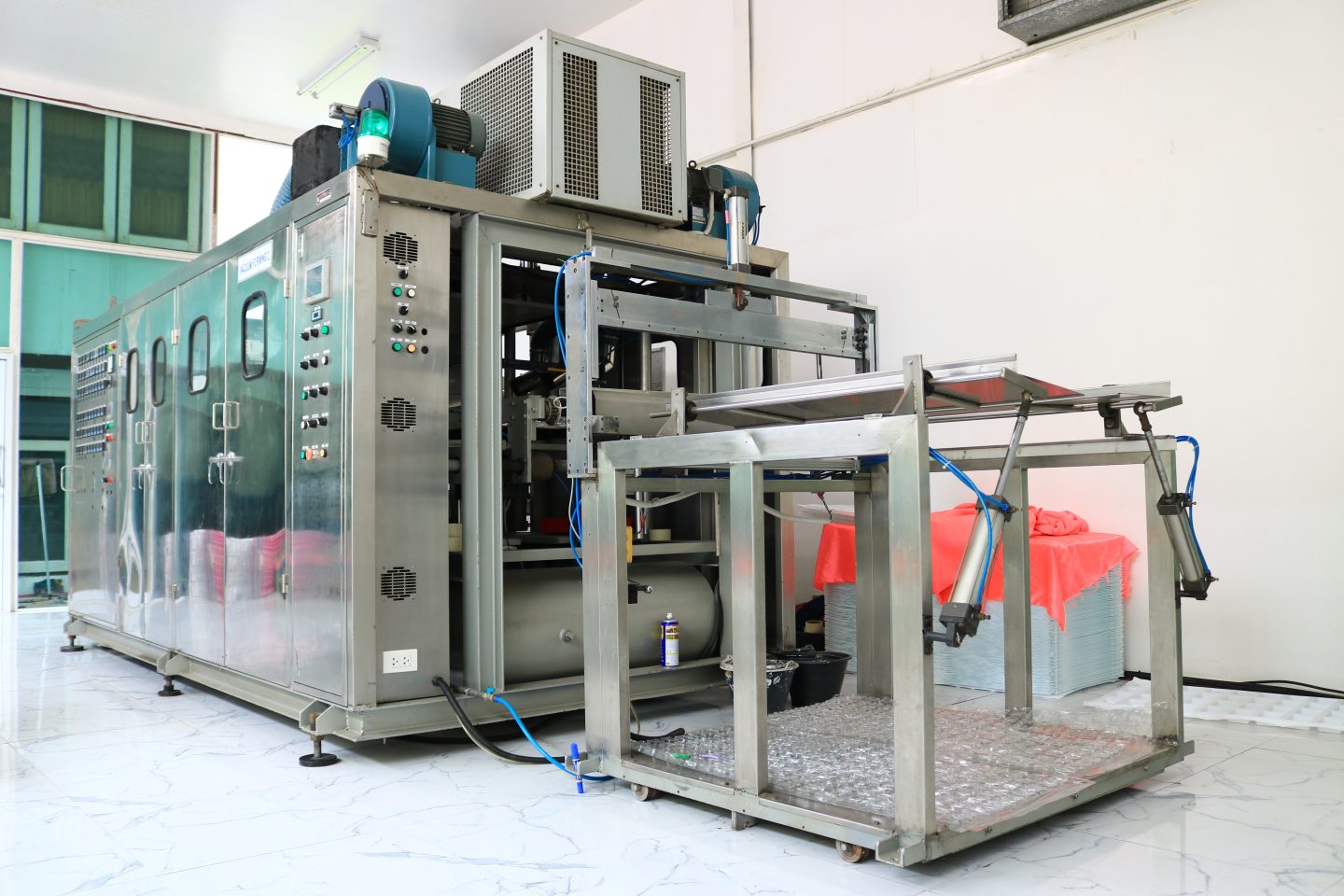
Ograniczenia termoformowania
Chociaż termoformowanie ma różne zalety, posiada również szereg ograniczeń. Rozpoznanie tych ograniczeń gwarantuje, że producenci będą mogli podejmować świadome decyzje, optymalizując swoje strategie produkcyjne.
- Ograniczenia materiałowe: Nie wszystkie tworzywa sztuczne nadają się do procesu termoformowania. Niektórym materiałom brakuje właściwości umożliwiających skuteczne formowanie pod wpływem ciepła i ciśnienia.
- Złożoność projektów części: Termoformowanie ma pewne ograniczenia, jeśli chodzi o skomplikowane elementy projektu. W przeciwieństwie do innych procesów, osiągnięcie bardzo szczegółowych lub skomplikowanych geometrii może być wyzwaniem. To ograniczenie oznacza, że produkty wymagające niezwykle szczegółowych komponentów mogą wymagać dodatkowych procesów lub alternatywnych metod produkcji.
- Grubość i konsystencja ścianek: Jednym z głównych wyzwań związanych z termoformowaniem jest utrzymanie jednolitej grubości ścianki, szczególnie w przypadku głębszych tłoczeń lub bardziej złożonych form. Charakter procesu może prowadzić do cieńszych ścianek w niektórych częściach uformowanego produktu. Ta niespójność może mieć wpływ na integralność strukturalną produktu i ogólną jakość.
Zastosowania termoformowania
Wszechstronny charakter termoformowania nadaje się do różnych gałęzi przemysłu, oferując rozwiązania dostosowane do konkretnych wymagań. Jego zdolność do formowania tworzyw sztucznych w różnorodne formy i struktury stanowi przełom w wielu sektorach.
Przemysł opakowaniowy
Termoformowanie jest kluczowym procesem w sektorze opakowań. Tworzenie tacek termoformowanych zapewnia zabezpieczenie produktów podczas transportu, minimalizując potencjalne uszkodzenia. Co więcej, opakowania blistrowe, stosowane głównie w opakowaniach do żywności i farmaceutyków, są świadectwem precyzji termoformowania, ponieważ opakowania te szczelnie otaczają poszczególne przedmioty, zapewniając ochronę i widoczność.
Zamykane opakowania, kolejny produkt termoformowany, to solidne rozwiązania opakowaniowe, szczególnie w handlu detalicznym, zabezpieczające przedmioty przed zanieczyszczeniami zewnętrznymi.
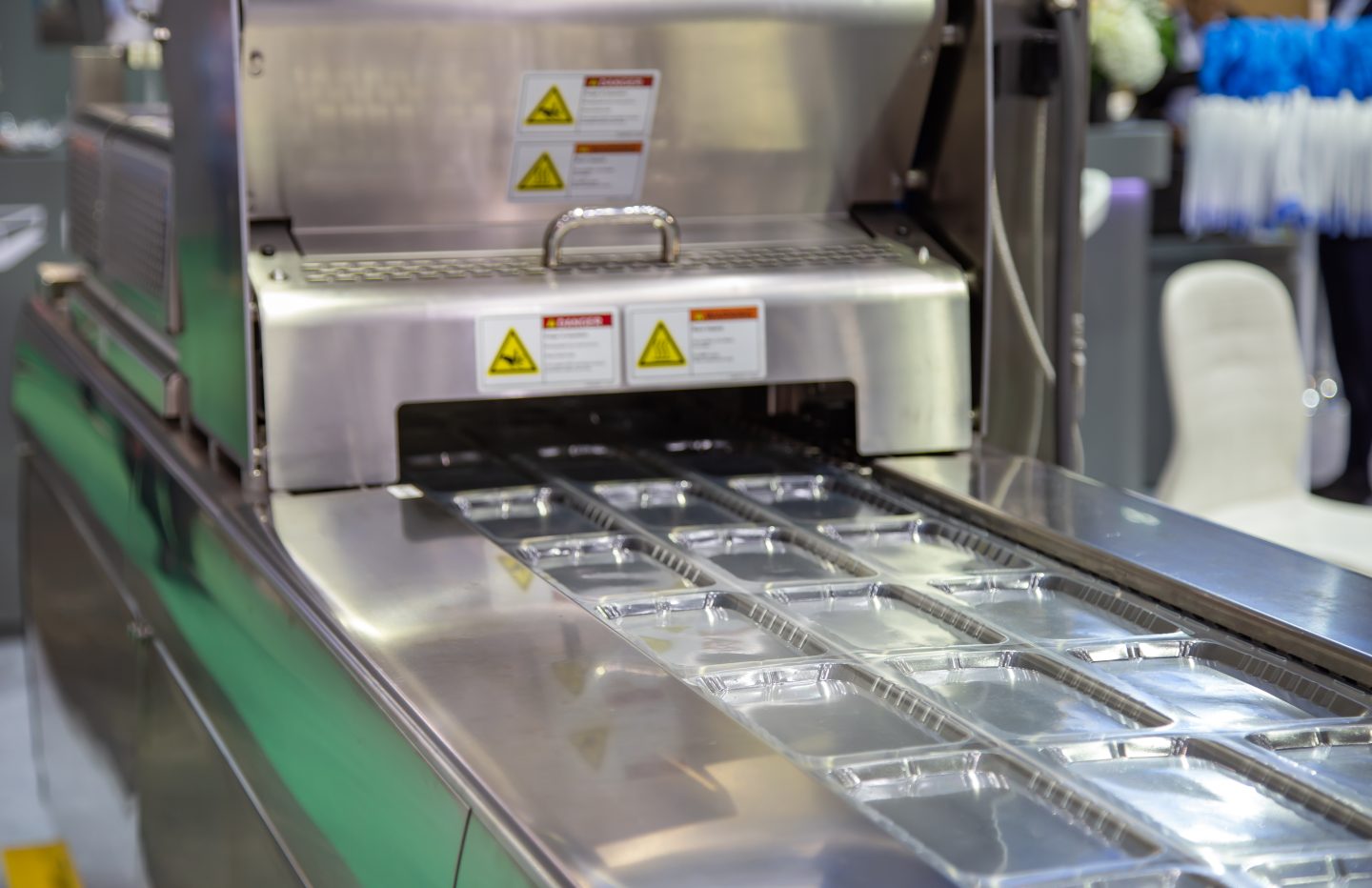
Branża motoryzacyjna
Przemysł motoryzacyjny szeroko wykorzystuje termoformowanie ze względu na jego niezliczone korzyści. Elementy takie jak panele drzwi i deski rozdzielcze wymagają trwałości połączonej z wyrafinowanym wykończeniem. Termoformowanie ułatwia tworzenie tych komponentów, gwarantując, że są one zarówno estetyczne, jak i funkcjonalne. W miarę ciągłego rozwoju pojazdów, w których wykorzystuje się zaawansowane technologie, wzrasta zapotrzebowanie na precyzyjnie formowane komponenty.
Opieka zdrowotna
W branży, w której najważniejsza jest precyzja i higiena, termoformowanie odgrywa ważną rolę. W opakowaniach wyrobów medycznych, niezbędnych do utrzymania sterylności, często wykorzystuje się tworzywa termoformowane. Dzięki temu urządzenia pozostają nieskażone i gotowe do użycia w razie potrzeby.
Co więcej, tacki na narzędzia chirurgiczne, uformowane tak, aby pomieścić określone narzędzia, są przykładem precyzji termoformowania. Tace te porządkują narzędzia i ułatwiają sterylizację, podkreślając znaczenie omawianego procesu w opiece zdrowotnej.
Dobra konsumpcyjne
Od zabawek, którymi bawią się dzieci, po pojemniki używane na co dzień w gospodarstwach domowych – wpływ termoformowania na sektor dóbr konsumpcyjnych jest ogromny. Proces ten umożliwia tworzenie trwałych zabawek, które wytrzymają próbę czasu. Z drugiej strony pojemniki korzystają ze zdolności termoformowania do tworzenia szczelnych zgrzewów, utrzymujących świeżość ich zawartości. Biorąc pod uwagę różnorodność towarów konsumpcyjnych, współpraca z Xometry oferuje najlepsze zastosowanie technik termoformowania.
Zastosowania termoformowania obejmują różne branże, stawiając czoła różnym wyzwaniom dzięki dostosowanym rozwiązaniom. Jego zdolność adaptacji gwarantuje, że pozostaje w czołówce metod produkcyjnych.
Termoformowanie a formowanie wtryskowe
Termoformowanie i formowanie wtryskowe to kluczowe metody produkcji tworzyw sztucznych. Różnią się jednak zasadniczo podejściem i zastosowaniem.
Termoformowanie polega na podgrzewaniu arkusza tworzywa sztucznego, aż stanie się giętki. Tak zmiękczony arkusz jest następnie formowany w określonej formie. Jest to proces idealny w przypadku dużych części oraz małych i średnich serii. Jego elastyczność, niższe koszty oprzyrządowania i możliwość szybkiej adaptacji prototypu to zalety. Jednak zazwyczaj ogranicza się to do prostszych projektów i często generuje więcej odpadów materiałowych.
Z drugiej strony formowanie wtryskowe wtłacza stopione tworzywo sztuczne do formy pod wysokim ciśnieniem. Proces ten doskonale nadaje się do tworzenia skomplikowanych projektów i najlepiej nadaje się do produkcji na dużą skalę. Produkty końcowe charakteryzują się stałą jakością i wąskimi tolerancjami. Główną wadą jest wyższy początkowy koszt oprzyrządowania, co czyni go mniej ekonomicznym w przypadku mniejszych serii.
Formowanie wtryskowe | Termoformowanie | |
Zakres ilościowy | 50 – 1 000 000 | > 1 |
Próbka | Ponad 1 miesiąc | Ponad 1 miesiąc |
Prototypowanie | ✔ | ✔ |
Produkcja wielkoseryjna | ✔ | ✘ |
Funkcjonalność | ✔ | ✔ |
Estetyka | ✔ | ✔ |
Złożone geometrie | ✔ | ✘ |
Kolorowe części | ✔ | ✔ |
Wybierając jedną z tych metod, należy wziąć pod uwagę złożoność produktu, wielkość produkcji i ograniczenia budżetowe. Obydwa procesy mają swoje zalety, ale decyzja często zależy od konkretnych wymagań danego projektu.
Realizuj zamówienia produkcyjne za pomocą termoformowania wraz z Xometry
Proces termoformowania jest kluczową metodą w dziedzinie produkcji, oferując wszechstronne rozwiązania w zakresie kształtowania różnych materiałów. Możliwość dostosowania do różnych branż, w tym motoryzacyjnej, medycznej i opakowaniowej, podkreśla jego praktyczność.
W przypadku firm poszukujących niezawodnych rozwiązań dla produkcji nisko- i średnionakładowej Xometry oferuje najwyższej klasy usługi termoformowania.