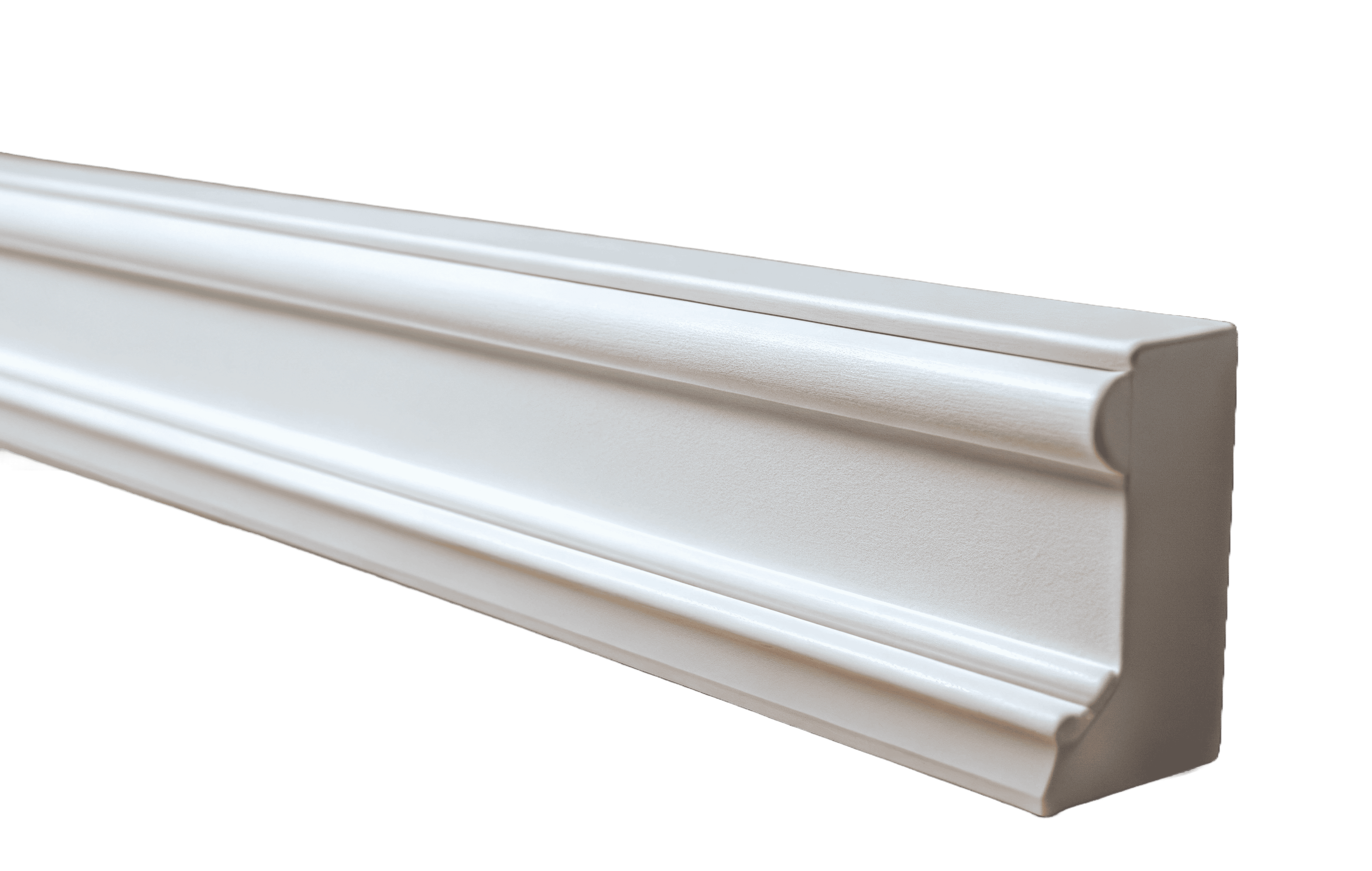
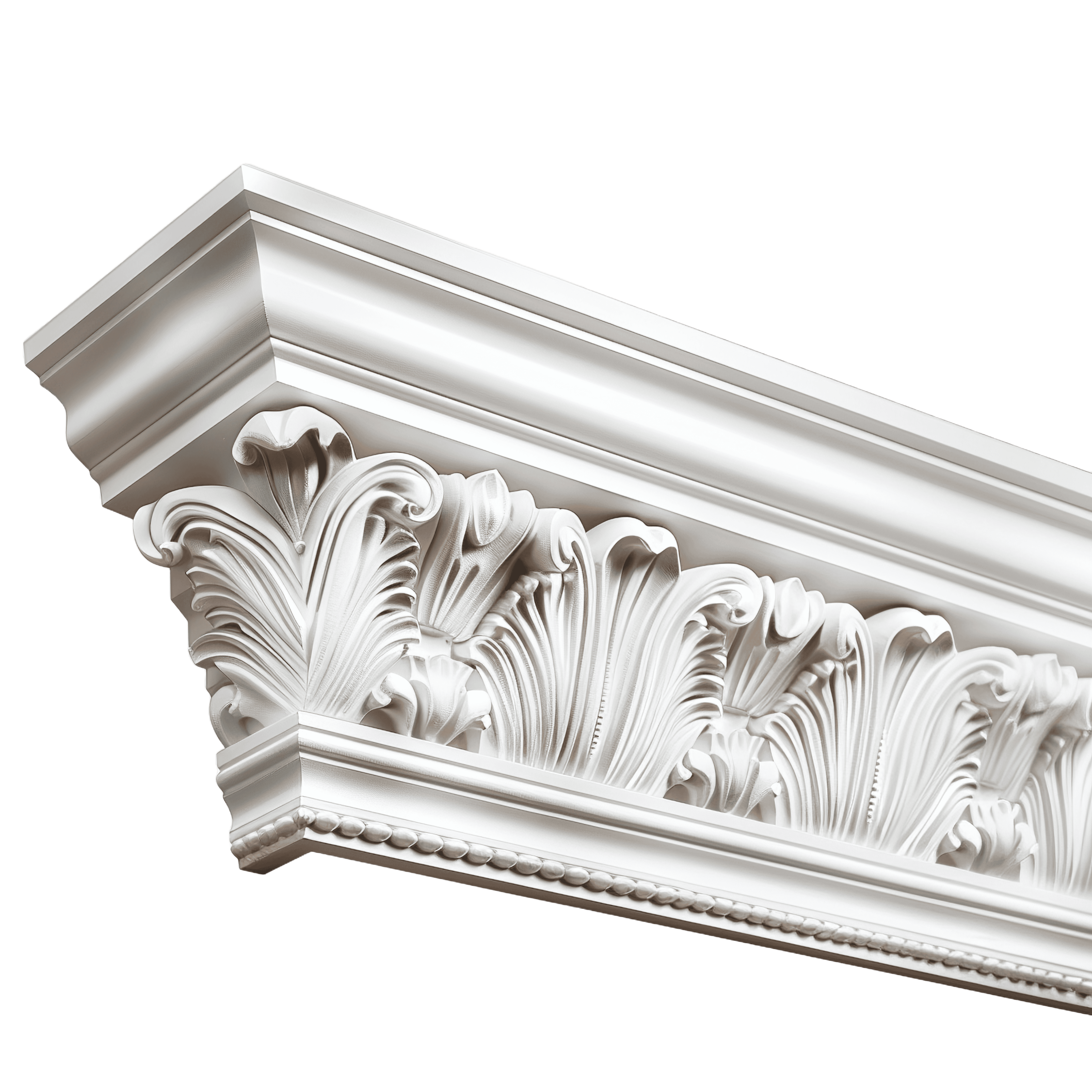
Foam Moulding Services
Source your custom structural foam moulding projects with Xometry, from lightweight yet durable components to complex geometries. Our foam molding process produces lightweight parts with a rigid outer skin, combining strength, design flexibility, and suitability for large panels, enclosures, and ergonomic supports. Our expert support at every stage, combined with attentive customer care, guarantees a seamless experience from quoting to order tracking.
Cost-effective production with lower tooling and material costs
Ideal for large, lightweight parts with high strength-to-weight ratio
Enhanced design flexibility for intricate shapes and long flow lengths
Low tooling and material costs
What is Foam Moulding?
Foam moulding is a manufacturing process that injects gas-impregnated plastic into a mould, creating parts with a lightweight foam core and a dense, rigid outer skin. This process delivers high strength-to-weight ratios, excellent durability, and design flexibility, making it ideal for large, complex components that traditional injection moulding cannot achieve. Foam moulding is widely used in industries such as automotive (lightweight panels, enclosures), construction (insulated panels, durable housings), medical (equipment casings, ergonomic supports), and industrial applications (storage containers, machine housings).
Technology Specifications
Our Manufacturing Capabilities
- Quantity: From 50 parts
- Materials: EPP (Expanded Polypropylene), EPS (Expanded Polystyrene), EPO (Expanded Polyolefin)
- Finishes: As moulded
- Tolerance: Depend on a part density and part design. Should be discussed during the DFM stage of a project
Tooling Design Engineer, BMW
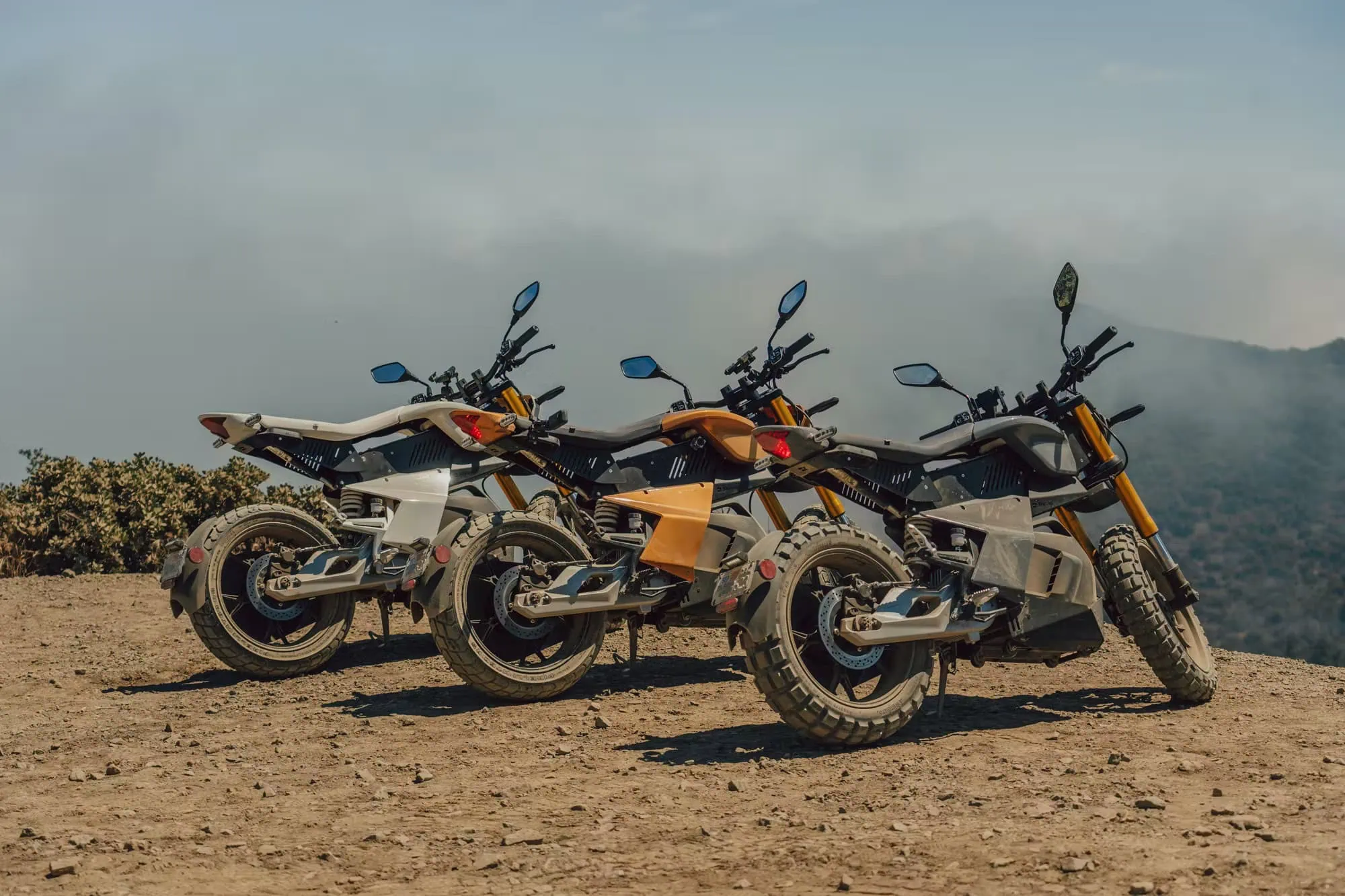
“Xometry delivers professionalism and ease. They take care of fulfillment so I don’t need to juggle or manage suppliers. We buy the quote and Xometry takes care of the rest.”
The Easiest Way To Manage Your Projects
1. Submit Your Foam Moulding Enquiry
Upload your designs, select the quantity, materials, surface finish, and other parameters, then submit a quote request.
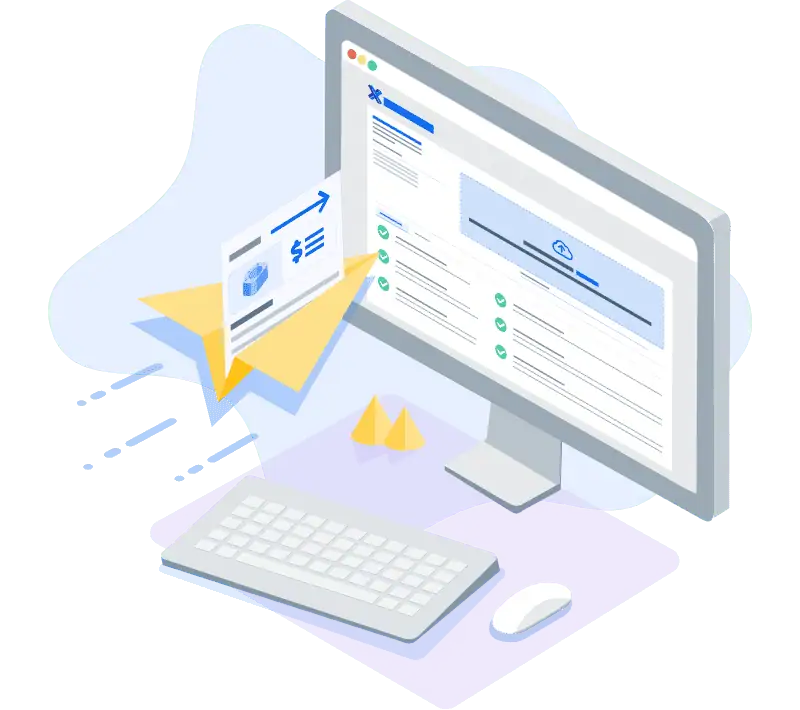
2. Review and Quoting
A Xometry engineer reviews your enquiry within 24-48 hours to ensure all requirements are met. You receive an initial quote. Upon your approval, our engineers match your project with the most suitable manufacturer based on skills, availability, and other criteria. We then send you a final quote.
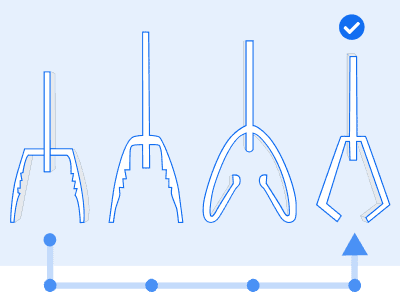
3. Project Kick-Off and DFM
Once you approve the final quote, you receive an order confirmation and an invoice for 50% of the mould costs. After that we start the Design for Manufacturability (DFM) process. Xometry works with you to clarify and finalise all technical details before proceeding.
4. Mould Building and Sample Production
After finalising DFM, we set deadlines for mould building and first sample production (T1). Our project manager oversees logistics and communication. You receive the T1 samples with a measurement report for approval. Feedback on the T1 samples should be received within 10 days and if further improvements might be required, further iterations (T2, T3, etc.).
5. Full Production and Delivery
Once samples are approved, Xometry manages full-scale production, quality control, and part delivery. You pay the production costs upon receiving the parts.
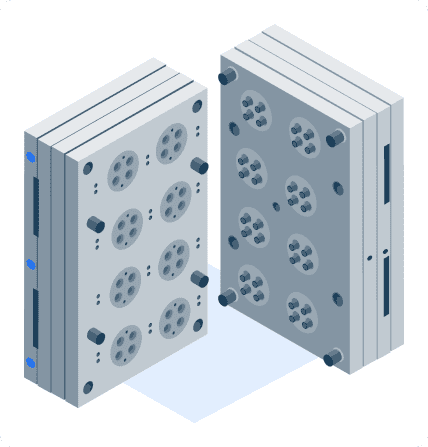
6. Mould Ownership and Re-Orders
The mould lifespan is between 10,000 to 1,000,000 shots. The mould is owned by you and maintained by Xometry. The customer can easily re-order parts whenever required.
The Advantages of Our Digital Manufacturing Platform
Massive Network Capacity
Access the production capacity of over 2,000 qualified manufacturers in Europe and 10,000 worldwide, offering a wide range of production capabilities and certifications. Our extensive network enables the production of parts with any level of complexity, in almost any material, with precise tolerances and the required post-processing.
Human Expertise Behind Every Order
Our experienced team ensures smooth order management at every step. From initial design checks to seamless communication with manufacturing partners, we provide personalised feedback and suggest design improvements to optimise your parts and production processes.
Flexible Purchasing Solutions
Xometry offers flexible post-payment options for reliable corporate customers, a variety of payment methods to suit your needs, and the ability to establish framework agreements for specific prices and quantities, ensuring cost predictability and streamlined procurement processes.
Quality Assurance
Xometry is ISO 9001:2015 certified. Our seamless Manufacturing Supplier Network integration, in-house applications engineering team, and Xometry Quality Assurance Lab ensure we back every part we ship with top-notch quality.
Fast Delivery across Europe
Xometry delivers parts to all European countries, including the UK, Norway and Switzerland. See your delivery options for instant quotes right away or plan your custom shipments for complex projects.
Certifications & Inspection Reports
Xometry can provide various certificates (compliance with order types 2.1 and 2.2, raw material certificates for metals and plastics, heat treatment protocols, RoHS certificates, etc.) and inspection reports (CMM, First Article Inspection Report – FAIR, measurement reports, etc.).
Available Materials for Foam Moulding
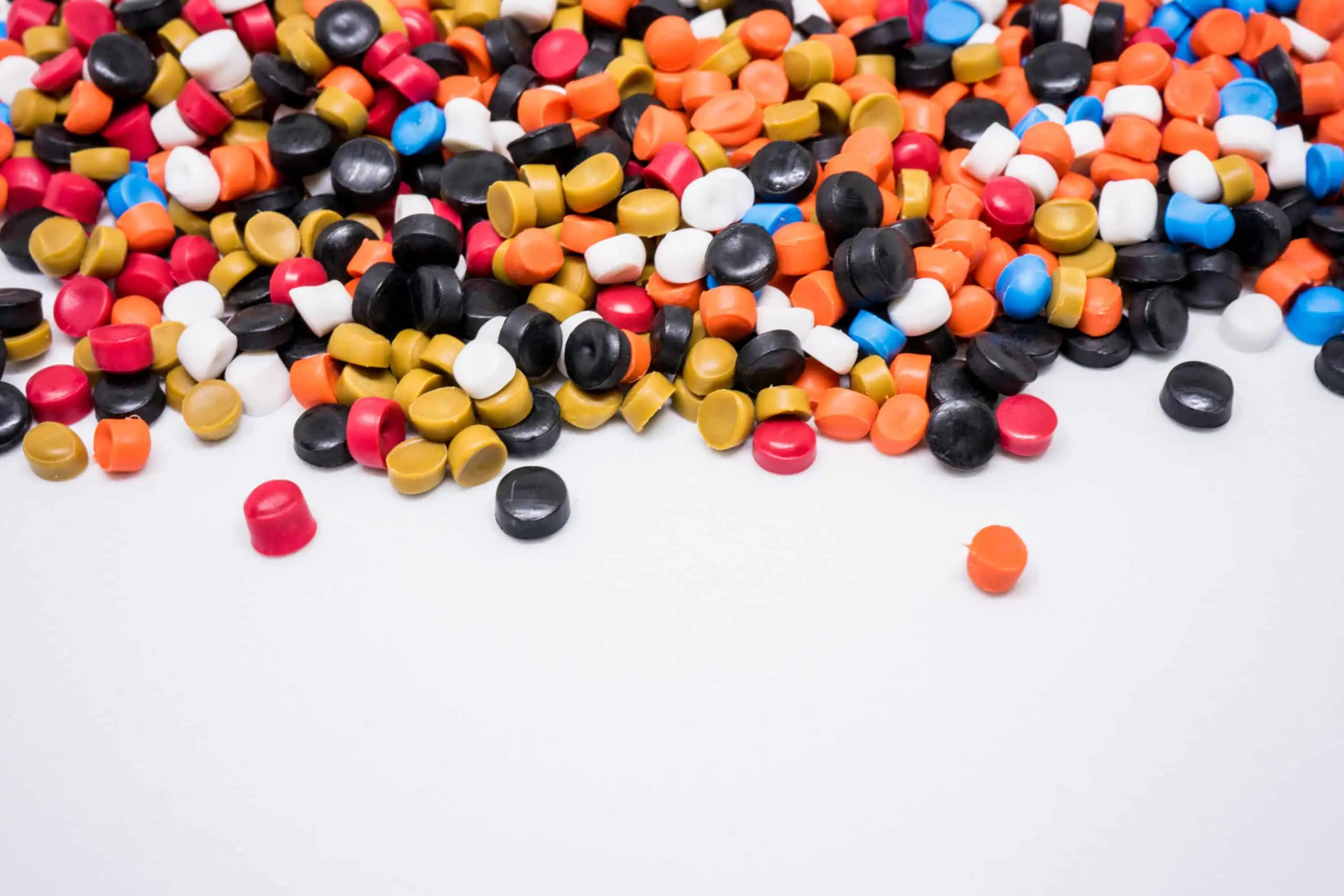
Plastics
- EPP (Expanded Polypropylene)
- EPS (Expanded Polystyrene)
- EPO (Expanded Polyolefin)
Stefano Grigis, Asitech
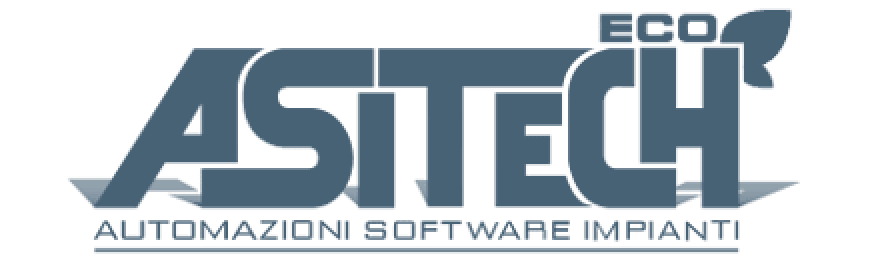
Stefano Grigis, Asitech
“We very much appreciated the speed of the platform: in zero time, I can get a quote for 1, 10 or 100 pieces, and test how much it might cost to produce with one material over another, which is crucial in the design phase but also to make realistic proposals for our customers.”
Frequently Asked Questions
Foam moulding is a manufacturing process that uses gas or chemical blowing agents to create lightweight, durable, and impact-resistant foam parts. This method is commonly used for protective packaging, insulation, cushioning, and structural components. Foam moulding is widely applied in industries such as automotive, aerospace, construction, medical, and consumer goods.
Products made through foam moulding include packaging inserts, insulation panels, automotive seating, and custom-shaped cushions. This process is ideal for producing lightweight components with excellent shock absorption, thermal insulation, and sound-dampening properties.
Common materials used in foam moulding include polyurethane (PU), expanded polystyrene (EPS), expanded polypropylene (EPP), and polyethylene foams. Each material offers different benefits, such as flexibility, rigidity, or high impact resistance.
Yes, we specialize in custom foam moulding, allowing us to create parts with unique shapes, densities, and mechanical properties tailored to your specific application. We can also provide design assistance to optimize your parts for cost and performance.
The maximum part size depends on the material and moulding method. Large-format foam moulding is possible for applications such as protective packaging, insulation, and structural components. Contact our team to discuss your specific size requirements.